Optimizing Advances In Bioprocess Liquid Manufacturing
Executive Summary
Manufacturing biopharmaceuticals is a complex process that presents a range of challenges in areas such as stability, consistency, predictability, potential for contamination, effective scale-up and quality versus yield.
Lot-to-lot variability is a common problem in bioprocess manufacturing, one that frustrates efforts to plan more effectively for downstream output. Pressure to achieve lot-to-lot consistency has intensified in recent years. This is partly due to more stringent regulatory requirements, in particular around trace metals. The pressure also reflects internal demand for manufacturing efficiencies, as biopharmaceutical companies grapple with issues such as rising drug-development costs and tougher barriers to market access.
“A lot of it is efficiency but we have had a great deal more regulatory requirements in more recent years, especially for trace metals,” comments Neva Alles, scientist, manufacturing sciences at Thermo Fisher Scientific. “The regulatory conditions for heavy metals have become more stringent. To be able to control the metals from a regulatory standpoint is important. But it’s also important for the customers, because the metals can have a significant impact on their cell cultures,” Alles explains.
Controlling Trace Metals
Trace metals may include aluminum, calcium, chromium, iron, magnesium, copper manganese, nickel and zinc. Thermo Fisher’s R&D team is working on understanding how, even at low levels, small shifts in the concentration of these metals may have a substantial bearing on cell growth and performance. An even more crucial issue than the addition of potential metal contaminants to cell-culture media is lack of control over them in the face of lot-to-lot variations.
In an effort to reduce this inconsistency, Thermo Fisher Scientific has developed new technology for the manufacture of liquid cell-culture media. “I’ve noticed over the years that the biopharmaceutical industry gets quite a bit of lot-to-lot variability in the whole manufacturing process,” Alles notes. “We’ve been able to find out a little more about what causes that. Part of this new approach to manufacturing is to try to improve that consistency lot-to-lot, so when there are manufacturing runs for biopharmaceuticals, our customers can plan their outputs and downstream processing better.”
Powder To Liquid
Historically, biopharmaceutical companies have used liquid cell-culture media for smaller-scale manufacturing (e.g., the earlier stages of clinical trials), transitioning to powdered media as production scales up to commercial volumes. The key is to maintain as much consistency as possible between these two formats. “What happens is, our customers generally develop their processes initially at smaller scale with our liquids, and then when they scale up they want to go to our powders. And sometimes they are seeing differences; that’s been a frustration,” Alles explains.
Acids And Bases
One current challenge in formulating liquid media is the traditional reliance, for the last three decades or so, on acids and bases as solubilizing agents. Acids and bases carry the risk of trace-metal contamination, inadvertent degradation, or undesirable chemical reactions, increasing the potential for lot-to-lot inconsistencies across bioprocess liquids. Thermo Fisher Scientific has therefore developed a new manufacturing process that enables it to significantly reduce the volume of acids and bases used in the manufacture of liquid cell-culture media.
“Right now we formulate our liquids, and I think its common practice, using acids and bases to help solubilize components,” Alles points out. “And moving forward, we’ve found a way to manufacture liquid media with minimal acid and base, with a reduction of up to 95%, by optimizing component forms and strategic management of the order of additions.”
This new process is being implemented in all Thermo Fisher’s Gibco™ liquid products under development and scheduled for launch during 2019.
Benefits Of Reduced Acid And Base
Among the benefits of minimizing acid and base use in liquid media is a reduced presence of trace metals, resulting in more consistent growth and productivity from lot-to-lot. “We’ve seen fewer metal contaminants in the liquid media, as well as less lot-to-lot variability,” Alles says. “So we reduce the contaminants and we reduce the inconsistency. The acids and bases often contribute to the contaminants and can cause inadvertent degradation or undesirable reactions.”
Better consistency can also drive process optimization, resolve complications with downstream processing and generate higher yields per batch. “We have actually seen slightly increased productivity in our tests, as well as improvements in consistency,” Alles comments.
Cell Growth And Productivity
In tests of Thermo Fisher Scientific’s Gibco™ CD CHO new liquid medium, the company’s CHO-S (Chinese Hamster Ovary Suspension) cell line showed growth of approximately 130% compared with liquid media made using the traditional liquid manufacturing process.
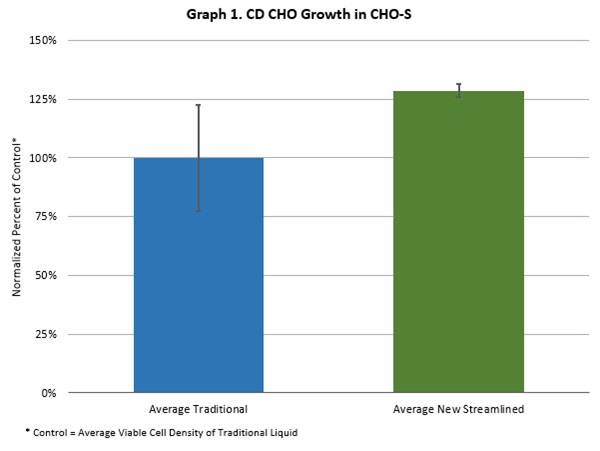
Lot-to-lot variability was reduced by 20% in terms of growth with the new streamlined liquid media versus the traditional CD CHO liquid media. CD CHO cell productivity almost doubled using the new manufacturing approach.
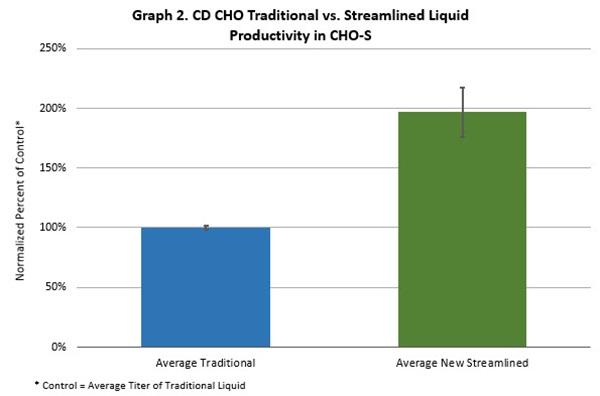
Tests also showed that cell-growth performance with the streamlined CD CHO liquid media was aligned with that of powder-based CD CHO AGT
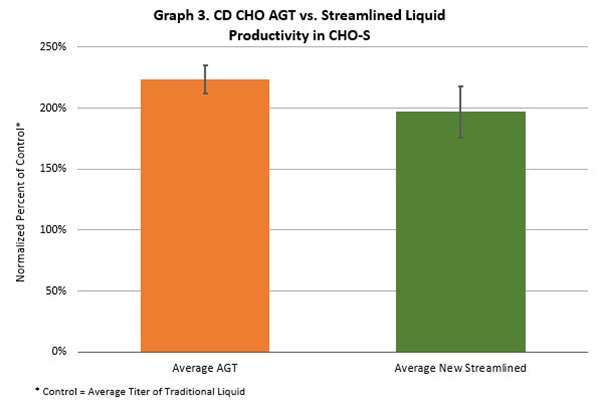
Quality, Performance, Cost Management
All of these improvements have clear implications for quality, performance and cost management in an increasingly competitive environment for biopharmaceutical manufacturing.
“It’s definitely a financial issue,” Alles states. “Any time our customers can get more yield out of each batch or production run, and consistently achieve that predicted yield, that is exactly what they want for high-quality production.”